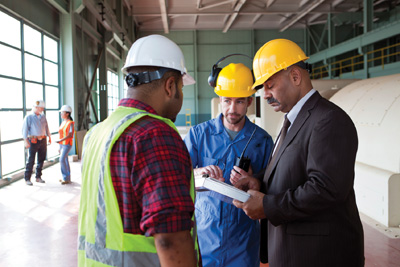
OSHA OSHA OSHA
OSHA is a highly charged topic.
And it might be a poor choice to start a safety tips article with OSHA.
But really, OSHA is the beginning, the middle and the end for worker safety.
OSHA Rules and Guidelines
The Top OSHA Rules Violations
So here are some of the most common manufacturing-related OSHA Rules violations:- Lockout/tagout
- Machine guarding
- Electrical, general requirements
- Respiratory protection
Lockout/Tagout
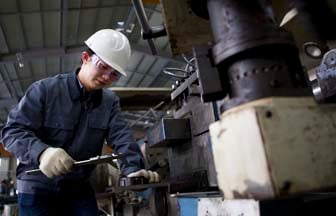
As you know, machineries' moving parts, heavy weight, heat and energy sources become a dangerous combination when operated incorrectly. For example, there were an estimated 5 million disabling injuries in 2009, and 280 deaths manufacturing machinery .
Lockout/tagout problems in food processing and manufacturing alone led to 28 deaths and 227 serious injuries like amputations from 2003-2013. In 2012, the same industry had 18,620 lost time injuries costing $1.4 billion.
7 Things to do for a Successful Lockout/tagout System
● Written procedures
● Documentation of each source of energy
● Locking and tagging devices
● Verification of energy isolation
● Proper locks at proper places (isolation points)
● Training (including skills demonstration) in the primary language(s) of employees.
● Auditing of work process
The cost of lockout/tagout procedures is far outweighed by the bigger costs created by avoidable accidents and injuries. For example, improper lockout/tagout safety measures led to death of a worker and a million dollar fine for a manufacturing company in South Dakota.
Forklifts and other Powered Industrial Vehicles
According to the Bureau of Labor Statistics (BLS) Census of Fatal Occupational Injuries, there are approximately 34,000 injuries and about 100 fatalities because of forklift vehicle accidents each year. Total "lost work days" --a critical metric in manufacturing -- from forklift accidents is huge. One study of 916 powered industrial vehicle accidents showed that they resulted in a total of 22,730 lost workdays for the next work year.5 Tips for Forklift Safety
OSHA has published many tips for improving forklift safety. Here are the top five:- Secure the load so it is safely arranged and stable. [29 CFR 1910.178(o)(1)] Do not carry damaged merchandise unless it has been secured by wrapping or banding.
- Center the load as nearly as possible. [29 CFR 1910.178(o)(1)] Use caution when handling off-center loads that cannot be centered. [29 CFR 1910.178(o)(1)] Distribute the heaviest part of the load nearest the front wheels of the forklift.
- Do not overload. Know the stated capacity of your forklift and do not exceed it. [29 CFR 1910.178(o)(2)] Only by keeping within the weight limit can you operate the forklift safely.
- A forklift's capacity is rated for a specified load center. If the load is off-center, improperly distributed, or oversized, it may exceed capacity and unbalance the forklift.
- Use the load extension backrest.
Machine Guarding
Below are some machine guarding tips from OSHA.
-
Guarding Enclosures:
Revolving barrels, containers, and drums must be guarded by an enclosure interlocked with the drive mechanism, so the barrel, gun, or container cannot revolve unless the guard enclosure is in place. [29 CFR 1910.212(a)(4)] -
Machine Anchoring:
A machine designed for a fixed location must be securely anchored to prevent it from walking or moving. [29 CFR 1910.212(b)] -
Protection Gear:
Eye and face protection must be provided to and worn by each employee when they might be exposed to eye or face hazards from flying particles. [29 CFR 1910.133(a)] -
Energy Control Program:
The employer must establish an energy control program consisting of energy control procedures, employee training, and periodic inspections to ensure that before any employee performs any servicing or maintenance on a machine or equipment, the machine or equipment is isolated from the energy source and rendered inoperative. [29 CFR 1910.147(c)(1)]
Electrocutions
From 1992-2003 there were 1,715 deaths in all trades that involved electricity.Below are 5 safety tips for preventing electrocutions.
-
Create Awareness and Dispel Electricity Myths:
It is critical to understand that a large amount of electricity is not required to cause death: “Many workers know that the principal danger from electricity is that of electrocution, but few really understand just how minute a quantity of electrical energy is required for electrocution. In reality, the current drawn by a tiny 7.5 watt, 120-volt lamp passed from hand to hand or hand to foot across the chest is sufficient to cause electrocution.The number of people who believe that normal household current is not lethal or that power lines are insulated and do not pose a hazard is alarming.” -
Insulated Tools:
In an area with potential electrical hazards, use insulated tools and wear protective clothing to reduce risk of shock. -
Surveying Work Area:
Identify all electric shock and arc flash hazards in your work area before starting to work. -
Equipment Isolation:
Make sure equipment is properly isolated from energy sources, if that is required. - Wait Until Lockout/Tagout Procedures are Completed: Until lockout/tagout testing and ground procedures are conducted, always treat unpowered equipment as though it was still powered.
Respiratory Protection
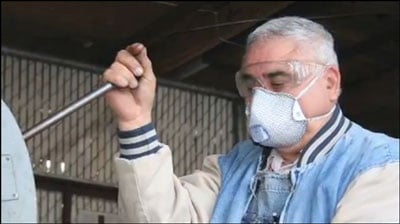
In 2008, private sector companies and government agencies reported more than 22,000 cases of occupational lung illnesses in their workforces. There are a wide variety of lung illnesses reported in different work environments. Occupational asthma, black lung, brown lung, asbestosis and mesothelioma are among the most common and severe respiratory illnesses. Respiratory protection limits these risks significantly.
-
Training:
Train workers consistently and properly to use respiratory protection and have refreshers. -
Use Correct Equipment:
Know which equipment to use for the right amount of protection. For example, a respirator must have a working filter to be effective. -
Proper Fit:
Make sure any respiratory protective device fits properly. -
Evaluate Asthma Risks:
Don’t assume that workers with a pre-existing conditions like asthma will be safe because they are wearing a respirator. -
Use Current Equipment:
Use current respiratory protection equipment only, because outdated equipment might be faulty or not effective enough.
Why Do Safety?
The financial and operational incentives to promote safety are significant. Employers pay billions every year in Worker’s Compensation for lost work days. Productivity suffers as well. But let's get specific about safety.
What do the numbers show? And what are the benefits?
50% Less Lost Workdays
According to OSHA, businesses that focus on protecting workers have about 50% fewer lost workdays. The U.S. Department of Labor has an online calculator to help you estimate how much a worker accident might cost. While this data is based on estimates, it’s important to use such calculations as a ballpark estimate of the magnitude of the problem, not an exactly calculated cost for your business. Here are some numbers to consider. The average occupational death costs $910,000. A lost workday case involving injury can cost an estimated $28,000, according to the calculator. If this figure seems too high, research has identified a range of $14,000 to $131,000. Estimated costs include medical treatment. Add in hospital time, rehab, and home health care and costs add up quickly. Confirmed ROI
The return-on-investment for proper safety programs is well proven.
“Numerous studies have put the return on investment (ROI) of such programs at 3:1 or higher. In a 2008 Indianapolis Business Journal article, trucking industry leader Celadon attributed a 20% reduction in healthcare costs to its Highway 2 Health initiative. And Federal Motor Carrier Safety Administration’s 2007 Commercial Truck and Bus Safety Synthesis 15 reports that Waste Management Inc. discovered that slightly more than 10% of its employees used 80% of dollars spent on healthcare, workers’ compensation, absence and disability benefits. An integrated campaign targeting key risk areas has since delivered multi-year savings of more than $100 million. But, none of these programs are mandated by federal agencies.”
Research shows that the cost of not having a culture of safety will cost you a lot more than you will spend on safety programs. But there is more to it than that.
What Alcoa CEO Paul O'Neill once coined and demonstrated as "the ripple effect," has been called “positive corporate culture” by high-minded business professors and analysts.
The Vague "Positive Corporate Culture"
Here are some typical areas of your company culture that can yield significant performance improvement:
Outward Performance
- Sales
- Customer Service
- Product Safety
- Product Quality
- Corporate Identity and Communications
Inward Performance
- Customer Retention
- Employee Retention
- Productivity
- Safety
- Employee Training
Why is this important?
Working With OSHA: Nightmare or Opportunity?
Before we suggest that OSHA can help your company, let’s address the rumors and fear-mongering about what a nightmare OSHA is.We’ve all heard OSHA lumped in with every other government regulation that’s hurting American business. In fact, we’re all heard bad stories about OSHA. It turns out these are more isolated anecdotes than ground truth.
What does the research say?
In a recent study, Harvard Business School researchers discovered that random OSHA inspections actually reduced a company’s injury rates by 9.4 percent over the longer term, versus uninspected firms. In addition, the study found that there is no additional cost to a company to comply with OSHA regulations.
On the other hand, fewer injuries led to a whopping 26 percent reduction in lost work days and medical expenses, for an average of $350,000 per company.
The study proved that OSHA regulations save rather than cost money.
Getting Started With OSHA Programs
According to OSHA, there are at two major reasons to partner:
"In a partnership, OSHA enters into an extended, voluntary, cooperative relationship with groups of employers, employees, and employee representatives (sometimes including other stakeholders, and sometimes involving only one employer) in order to encourage, assist, and recognize their efforts to eliminate serious hazards and achieve a high level of worker safety and health.
Company Safety Program Examples
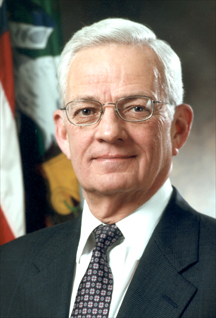
One of most important case studies in modern corporate history is Alcoa Steel under CEO Paul O’Neil’s leadership. "Until I said the target was zero, we didn't have a problem. Part of the role of leadership is to create a crisis."
His approach worked.
By 2000, it was five times safer to work at Alcoa than 10 years earlier. From the start, O'Neill sent a clear message to Alcoa's workers and managers. He often began his speeches at factories by pointing out the fire exits. He led by example, personally wearing hearing protection in noisy areas.
Consistency, O'Neill believes, is a vital part of leadership.
He warns against giving employees the notion that management will switch priorities as "…the flavor of the month. If you really want people to believe you," he said, "you have to be painfully consistent."
Values in Action
It’s easy to talk about values, or place posters on office walls with slogans, but then not walk the talk.Core values are created by a founder or CEO and they are an extension of her or his personal values.
O’Neil put worker safety first for two reasons:
- He wanted to reduce fatalities and injuries due to his own personal compassion
- He also knew it would be good for worker productivity, increase the company’s output and raise profits.
Nucor
“It’s what we focus on everyday. There’s nothing more important than our teammates, nothing more important than the safety of our teammates, and you gotta give ‘em the equipment so they can perform their tasks at the absolute most safest way,” says Nucor Vice President and General Manager Mike Lee.”
In 2012, Nucor had revenues of about $19.4 billion, and $245 million in profits in 2014. Listen to Nucor CEO Dan Dimicco describe in detail three keys to Nucor's success and profits.
Safety First
"Profits is not the first thing you can't have a profitable company if you're not running a safe company because you don't have the right mentality. If you're not safe, you're not going to be producing quality products, you're not going to be efficient because people are going to be afraid of where they work. They're not going to be giving everything they have, and you won't have the lowest costs. For all those reasons, you won't be profitable. We do all things for the long-term success of the company."Employee-oriented
"Another core value is being employee-oriented. We have a no-layoff practice even when things slow down. You can't build a loyal work force that's going to give you everything they have if, when times are bad, you say "we needed you then, we don't need you now. Go away, we'll call you back in six months." You can't have a practice like that unless you're the low-cost producer and take care of the customers."Hiring Right
"Another key to our success is hiring the right people. A lot of people say their most important resource is their people. I say no absolutely not. Your most important resource is the right people. Through your hiring and training, you attract the right people to your organization."
So if you are inspired to start or significantly improve your safety program, or create a strong culture of safety for your manufacturing firm, you will be faced with a challenge:
Getting all the elements in your company humming required to achieve a culture of safety.
In some ways, if we go back to "the ripple effect," safety is as safety does.
Improved safety might do more to grown profit at your company than you'd ever imagine.
It also might make it a great place to work.
What do you think is the greatest difficulty in creating a culture of safety for manufacturing companies?